Clean, Cut, Weld: Exploring 3 Major Industrial Uses of Laser
Laser, or Light Amplification by Stimulated Emission of Radiation, was a groundbreaking discovery that has been incorporated into various technologies and instruments.
With their unmatched precision, speed, and versatility, lasers have revolutionized modern industry. From manufacturing plants to high-tech workshops, lasers are now essential tools for a wide range of applications.
In this article, we will explore the three major industrial uses of lasers: welding, cleaning, and cutting. We will also explore how lasers are reshaping these tasks, offering more profound insight into the technology behind them and the advantages they bring.

Laser Cleaning vs. Laser Cutting vs. Laser Welding
What Is a Laser and How Does It Work?
Laser stands for Light Amplification by Stimulated Emission of Radiation. Lasers are optical devices that produce highly focused, special types of light. The device stimulates atoms or molecules to emit light at particular wavelengths and amplifies that light.
The light is limited to a narrow range of wavelengths (monochromatic) and consists of waves that are in phase with each other. Compared to traditional sources, such as a lightbulb or flashlight, laser light is focused and does not spread out much.
As a result, light can travel very long distances. In addition, they can concentrate a lot of energy on a tiny area, which is crucial in industrial applications such as welding, cutting, or cleaning.

How Do Lasers Work?
Source: https://www.youtube.com/watch?v=CJ7ak46P3iE
Types of Laser
Laser energy is extracted from several different sources, including gas, solid, optical fiber, or UV light. Most commonly, lasers are divided into two primary groups: gas lasers and solid-state lasers.
The most commonly used lasers in industry are:
-
CO2 lasers (gas lasers): The laser energy is extracted from a gas mixture of carbon dioxide, helium, nitrogen, xenon, and hydrogen, which are electrically excited. These lasers are cheap, but less energy efficient than newer types. However, CO2 lasers are still widely used on thermoplastics and organic matter (wood, leather, etc.)
-
Solid-state lasers: Solid lasers use crystal lattices as an active medium instead of gas mixtures. The most common type is the Nd: YAG laser, which uses neodymium-doped yttrium-aluminum garnet crystals. The crystals are excited by lamps or diodes and emit laser radiation. YAG lasers are suitable for most metals, even reflective ones, and some plastics, but are expensive to maintain and use.
-
Fiber lasers: These use optical fiber as the gain medium, which makes them ideal for precision tasks. Optical lasers can fire tiny spot sizes, making them suitable for applications that require high powers and excellent precision.
-
UV lasers: UV/IR lasers are newer types. These lasers generate laser beams by using high-energy photons in the ultraviolet or infrared spectrum, making them super efficient and energy-potent.
-
Semiconductor laser (LD: laser diode): This type of excitation features a narrow emission spectrum, and it can be triggered by selecting the specific absorption transition of the laser medium. It provides high absorption efficiency and excellent beam convergence for high-density excitation.

Applications of Lasers
Laser light yields various unique properties such as coherence, monochromacy, directionality, and high intensity. These unique properties make lasers useful in multiple applications, such as the following:
-
Medicine: Lasers are used in medicine for surgery, kidney stone removal, cancer diagnosis and treatment, endoscopy, cosmetic treatments, to produce plasma or chemical reactions, and more.
-
Communications: People use lasers in communications to send information over large distances, underwater communication networks, and space communications.
-
Industry: Workers use lasers to cut, weld, or clean metal pieces, for heat treatment, photolithography, or engraving.
-
Science and technology: Lasers allow scientists to count the number of atoms in a substance, retrieve stored information from a CD, burn CDs, measure pollutant gases, for computer printers, detect earthquakes, etc.
-
Military: Soldiers use lasers as range finders, to sense and measure minimal angles of rotation, to dispose of the energy of a warhead, as secretive illuminators for reconnaissance during night, and more.

Source: https://northslopechillers.com/blog/lasers-the-cutting-edge/
This is an indefinite list, as technological improvements include lasers in more fields of life every day. You can find lasers in supermarkets to read barcodes, laser car wash stations, holographs, and many, many more. However, we will further focus on the three primary industrial uses:
-
Cleaning
-
Cutting
-
Welding

Examples of Laser Welding, Cleaning, and Cutting Projects
Source: https://www.stylecnc.com/laser-welding-machine/3-in-1-laser-welder-cleaner-cutter.html
Laser Cleaning - What Is It and How Does It Work?
Laser cleaning is a form of ablation that uses laser energy to remove a selective surface layer from a metal. Fabricators use it to remove contamination from the metal surface, such as rust, paint, coating, or oxide layer, with extreme precision without damaging the metal underneath.
Like other laser methods, cleaning uses a focused beam of light. But in cleaning, the beam covers a larger area. Lasers use a technique known as laser scanning, which rapidly scans a laser beam along a path or across a wider zone. As a result, lasers remove only targeted material for a fraction of a second at a time.

Laser Cleaning Process
Photo by@ peslaser.us11 (TikTok)
How Does Laser Cleaning Work?
Laser cleaning works by evaporating the selective surface layer of contamination, coating, or oxides. This evaporation occurs due to ablation. Each material has an ablation threshold, or the level of energy required to cause the breaking apart of solid materials.

How Laser Cleaning Works
Source: https://www.researchgate.net/figure/Schematic-of-the-laser-cleaning-the-rust-a-heat-from-the-laser-being-conducted-to-the_fig4_351509315
Each material has a different ablation threshold. Most common contaminants, such as rust, dirt, oil, or coatings, have much lower thresholds compared to bulk metals such as steel, stainless steel, or aluminum. So, by adjusting the parameters, you can precisely target the contamination without affecting the surface of the base metal.
The focused laser energy targets the contaminants, which absorb laser light. The energy turns contaminants or coating particles into a gas. Otherwise, the pressure of the interaction will cause particles to unstick from the surface.
Laser cleaning uses only laser beam energy, so there are literally no consumables. Lasers also use no chemical products or solvents, making laser surface cleaning one of the safest solutions for rust and coating removal. You only need a power plug to set up and be ready to go.

Laser Cleaning for Rust Removal
Photo by@ techinsider (TikTok)
Laser Cleaning Applications
Laser cleaning is a versatile and precise surface removal method, perfect for countless industrial applications. However, the most common applications today include:
-
Weld preparation: Lasers can create an immaculate surface for welding by removing rust, paint, oil, or dirt. Clean surfaces are a must for methods such as TIG welding.
-
Post-weld cleaning: You can use laser cleaning to remove oxides and other contaminants resulting from welding.
-
Cleaning surfaces to maximise paint adhesion.
-
Simplifying mold maintenance.
-
Increasing coating life by pre-cleaning.
-
Laser oxide removal from specialty alloy ingots.
-
Paint removal from defective parts that would be scrapped.
-
General metal fabrication.
In general, laser cleaning is helpful in all applications that require metals with immaculate, contamination-free surfaces.

Laser Cleaning the Pipe Surface before Welding
Source: https://www.thefabricator.com/thefabricator/article/finishing/an-introduction-to-laser-cleaning-and-laser-texturing
Advantages and Drawbacks of Laser Cleaning
Metal fabricators today use various metal cleaning methods, such as abrasion blasting, dry ice blasting, and chemical or thermal cleaning. While these techniques can be easier to use, laser cleaning provides various advantages:
-
Non-contact cleaning: Lasers are much less aggressive compared to traditional abrasive blasting, reducing the risk of potential damage and harm.
-
High precision: When tuned right, lasers are highly selective and can remove all contaminants, oxides, or coatings down to bare metal without damaging it.
-
High speed: Laser cleaning is a fast method that uses a scanning technique to cover large areas quickly. Depending on the metals and contaminants, lasers can clean up to hundreds of square inches of material per second.
-
Safe and sustainable: Lasers don't need additional chemicals or consumables to work. This principle makes laser cleaning a safe, clean, and sustainable process, as there is no waste. Chemicals won't damage your skin or respiratory tract.
-
Easy automation: Laser cleaning is easily automated and integrated onto the production floor.
-
Low operating cost: The process doesn't require cleanup, and it comes with low operating costs and low maintenance.
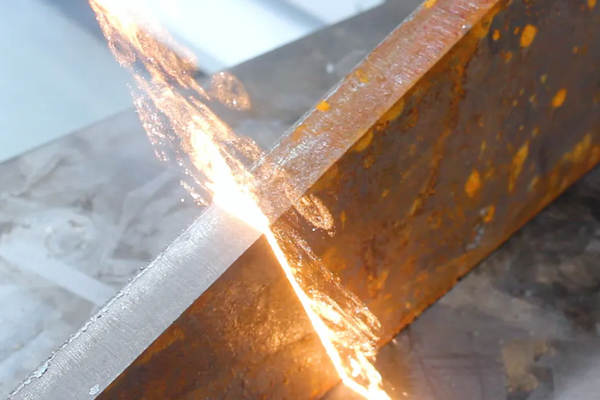
Source: https://hantencnc.com/blog/advantages-and-disadvantages-of-laser-cleaning-machines
However, each process has its drawbacks, so the most notable cons of laser cleaning are:
-
High initial investment: Laser cleaning equipment can be complex and expensive. Although it yields a high return by providing precise and fast cleaning, it presents a high initial investment.
-
Technically challenging: Operating a laser cleaning system requires a certain level of technical expertise.
-
Material limitations: Some materials can reflect or absorb laser energy inefficiently, making the cleaning process ineffective or slow. Although it can be used on various metals, it is not universally applicable.
-
Energy consumption: In large-scale, mass production, laser cleaning can be energy-intensive.

Rust Removal Using Laser
Photo by@ sciquestor (TikTok)
What Is Laser Cutting?
Laser cutting is a method that uses a highly focused and energized laser beam to evaporate and cut through metal surfaces. Optical fibers and mirrors transfer the laser light, and lenses focus it into a small spot. The smaller the laser dot, the higher the energy it carries.
Depending on the metal thickness, this energy is high enough to burn, melt, or evaporize the surfaces and cut through them. This principle yields exact, clean cuts with minimal waste (kerf), and fabricators also use it for boring and engraving.

Source: https://www.metalsupermarkets.co.uk/laser-cutting-metals/
How Does Laser Cutting Work?
Laser cutting works by directing and focusing the laser energy onto the metal surfaces. High-power lasers force a very small-diameter, high-energy light beam that pierces through metal surfaces. Cutting uses a CO2 laser (for cutting, boring, and engraving), Nd lasers for high-energy, low-repetition boring, and Nd: YAG for very high-power boring and engraving.
Mirrors or fibre optics transfer and direct the beam through a lens. The lens focuses the light, creating a laser beam that is typically smaller than 0.0125 inches. This small beam carries high energy density, which quickly evaporates the surfaces, creating a kerf as small as 0.004 inches.
Typically, cutting systems use a CNC (Computer Numerical Control) to direct the beam. The laser moves in pre-computed X and Y directions along the machine bed. A motion control system follows a CNC or G-code of the pattern, yielding accurate results.
In some systems, a high-pressure stream of gas blows the molten material out of the bottom to prevent it from fusing with the cut pieces. Conversely, high-power lasers vaporize all metal, so there is no need for gas.

How Does Laser Cutting Work?
Source: https://www.3dsculplab.xyz/Blog/post/What-is-metal-laser-cutting
What's The Maximum Laser Cutting Thickness?
The maximum cutting of the laser mostly depends on its power and the type of metal. The power of the laser directly dictates the amount of energy the laser beam can deliver. The reflectivity of the metal surface dictates how much energy it can absorb. Shiny metals tend to reflect the laser beam, requiring more energy to melt and evaporize.
For example, a 500W laser can cut up to 5mm (approximately 1/4") thick carbon steel. Meanwhile, due to reflectivity, it can only cut up to 2mm (approximately 1/16") thick copper, aluminum, or brass.
However, high-powered lasers reach a power of 40,000W. These high-powered systems can cut up to 100 mm (up to 4 inches) thick carbon steel, at up to 100 mm/s feed. Nonetheless, they can cut up to 70 mm of aluminum or 80 mm of stainless steel.

*Notice: The above data is for reference only. Cutting thickness and power may vary in actual production.
Advantages and Drawbacks of Laser Cutting
Advantages of Laser Cutting include:
-
High Precision and Accuracy: Laser cutting produces precise and clean cuts, ideal for intricate designs and tight specifications.
-
High Speed: Faster than many traditional cutting methods, especially for thin to medium-thickness materials.
-
Versatile: It is for a wide range of materials, including metals (carbon steel, aluminum, stainless steel), plastics, wood, glass, and composites.
-
Minimal Material Waste: A narrow kerf width means less material is lost, which contributes to cost efficiency.
-
Easy to automate: Easily integrated with CAD/CAM systems, improving repeatability and productivity.
-
Non-contact Process: Reduces mechanical wear and the risk of material deformation.

Source: https://www.rapiddirect.com/blog/sheet-metal-laser-cutting/
Drawbacks of laser cutting are:
-
High Initial Cost: Laser cutting machines and maintenance are expensive, making entry cost-prohibitive for some businesses.
-
Energy Consumption: Especially in high-power applications, laser systems can be energy-intensive.
-
Material Limitations: It is not suitable for very thick materials or highly reflective metals (like copper and aluminum) without specialized equipment.
-
Heat-Affected Zone (HAZ): Depending on the material and settings, this zone can cause minor thermal damage or distortion near the cut edge.

Source: https://www.emachineshop.com/science-behind-sheet-metal-cutting/
Laser Welding Explained
Laser beam welding is a metal joining process that uses the heat of the focused laser beam to melt and fuse the pieces. Compared to traditional arc welding methods, such as MIG welding or Stick welding, laser welding uses the heat of the laser beam to reach the melting point of metal surfaces.

What is Laser Welding?
Source: https://bccncmilling.com/what-is-laser-beam-welding/
Like other laser applications, laser welding is also a very precise method. It's focused energy narrows the heat-affected zone, which is crucial in avoiding warping or distortion on thin sheet metals.
LBW (Laser Beam Welding) is highly valuable in various industries because it works well with delicate, heat-sensitive metals and complex designs. Welders commonly use it in the automotive, aerospace, medical tool manufacturing, jewelry and watchmaking, and nuclear industries.

Pendant Repair Using Laser Welding
Source: https://www.riogrande.com/knowledge-hub/laser-welding-technology/
How Does Laser Welding Work?
Laser welding works by tightly focusing the laser light into the joint. It is like focusing sunlight through a magnifying glass to burn a piece of paper.
The heart of laser welding is the laser source that generates the laser beam. The raw laser beam carries an initial energy, but it is not high enough to melt the pieces.
Optical fiber and mirrors transport the laser beam. Lenses, such as a curved mirror or surface lens, focus the raw beam diameter to create a depth of focus. The focused beam is reduced to a spot size, which ranges from tens to a few hundred microns in diameter.
Focusing the raw light on tiny spot sizes creates extreme power density. Depending on the spot size, the density can reach the melting point of metal pieces, which will fuse as they solidify. However, the power is lower than that used in laser cutting, which completely evaporates the parts.

How Does Laser Welding Work?
Source: https://www.intechopen.com/chapters/80478
Laser Welding Types
Depending on the power density, there are two primary types of laser welding:

Conduction Laser Welding vs. Keyhole Laser Welding
Source: https://ebindustries.com/conduction-mode-and-keyhole-mode-welding/
-
Conduction laser welding: This type uses low-power lasers, typically rated less than 500W. The laser beam produces a power density of less than 105W/cm2, which is enough to melt and fuse the metal's surfaces. Due to the lower heat, this is a slower technique, best for thin pieces, but it yields high-quality results and aesthetically pleasing welds.
-
Keyhole laser welding: This is a fast and aggressive process that uses high-power lasers. The lasers produce a power density higher than 105W/cm2. As the laser melts, evaporates, and penetrates the metal, it forms a cavity known as the keyhole. This plasma-like state reaches extreme temperatures (over 17.000 F), which makes it ideal for high-volume production.
Based on the type of laser beam welding process, we also see types such as laser spot welding, laser seam welding, or hybrid laser welding. Particularly interesting is hybrid laser welding, which combines laser with traditional arc welding methods, such as TIG or MIG welding. It combines the advantages of both types of processes, yielding strong, precise, and high-quality welds.

What is Hybrid Laser Welding?
Source: https://www.sciencedirect.com/topics/engineering/laser-arc-hybrid-welding
Advantages and Drawbacks of Laser Welding
Advantages of laser welding include the following:
-
High precision: Laser welding produces extremely fine and accurate welds, especially in delicate or complex components.
-
High welding speed: The process is faster than traditional welding methods, especially for thin materials.
-
Can produce deep penetration: High-powered lasers can create deep-penetrating welds with a narrow weld seam.
-
Minimal Distortion: The focused heat input results in a smaller heat-affected zone (HAZ). Narrow HAZ minimizes warping and distortion.
-
Easy to automate: Easily integrated into automated systems and robotic arms for high-volume, repeatable production.
-
High weld quality and aesthetics: Lasers produce less spatter, fewer fumes, and require little to no post-processing. They yield highly aesthetic, clean welds.
-
Works in Difficult-to-Reach Areas: The laser can be directed via mirrors or fiber optics to work on complex designs and hard-to-reach areas.

Source: https://www.yupeclaser.com/how-thick-of-metal-materials-can-a-handheld-laser-welder-weld/
Drawbacks of laser welding include:
-
High Initial Costs: Initial setup, including the laser system and safety infrastructure, is expensive.
-
Issues with metal reflectivity: Welding highly reflective metals like copper or aluminum without special precautions can be challenging.
-
Requires precision and good weld preparation: Joint fit-up must be very accurate; gaps or misalignments can lead to poor weld quality.
-
Thickness Limitations: While excellent for thin to moderately thick materials, very thick sections may require multiple passes or other methods.

Source: https://www.accteklaser.com/what-factors-affect-the-weldability-of-laser-welding/
Final Thoughts
Laser technology has become a cornerstone of modern industrial processes, offering unmatched precision, efficiency, and adaptability in cutting, welding, and cleaning applications. While each use has its advantages and limitations, lasers' overall impact on productivity and quality is undeniable.
Whether improving weld integrity, achieving cleaner cuts, or eliminating surface contaminants, lasers are paving the way for smarter, faster, and more sustainable manufacturing practices. Their role in shaping the future of industry is only set to grow stronger.
🧐Clean, Cut, Weld: Exploring 3 Major Industrial Uses of Laser FAQ
1. What is laser cleaning, and what are its applications?
2. What are the advantages and disadvantages of laser cutting?
Leave a comment