How to Avoid Welding Burnback: Causes and Solutions
MIG welding is one of the most straightforward, beginner-friendly metal joining methods and is best for beginners and new welders. However, it is not uncommon to encounter welding defects during your journey.
Welding burnback is a specific defect that occurs in wire welding processes such as MIG or Flux-cored arc welding. The defect occurs once the welding wire fuses with the contact tip and clogs it.
In this article, we will provide helpful tips on how to avoid welding burnback and give a detailed explanation of the leading causes and solutions. We will help you save time and money on frequent buying and replacing contact tips in your MIG torch.

What Is Welding Burnback?
A welding burnback is a specific welding issue that occurs in welding methods that use a continuously fed wire. These are Gas Metal Arc Welding (GMAW) or MIG welding and Flux Cored Arc Welding (FCAW).

MIG Welding Diagram
Source: https://www.mechdaily.com/what-is-mig-welding/
Welding burnback occurs once the wire burns back inside the nozzle and fuses itself with the contact tip. The MIG welding arc climbs up the wire and fuses it to the contact tip of the welding gun.
This defect occurs due to the working principle of wire welding processes. Wire processes use a continuously fed wire that moves from the spool through a wire feeding mechanism, liner, and torch.
In MIG welding, the wire is also an electrode that transfers the current and forms the arc. If the arc doesn’t follow the feeding, it moves back towards the MIG gun. Once the arc meets the contact tip, it fuses the wire with it and blocks the small opening.

What is Welding Burnback?
Source: https://blog.binzel-abicor.com/usa/solving-welding-burnbacks-in-robotic-applications
What to Do if Burnback Happens?
Once the burnback occurs, the wire clogs and fuses with the contact tip. Depending on how much of the wire is fused, you can remove the nozzle and tip and file it. However, once the contact tip or the nozzle is damaged, it can interfere with the wire feed.
Inconsistent wire feed is the leading cause of various defects in MIG welding. Therefore, if the burnback occurs, we strongly recommend completely removing the old one and installing a new contact tip and nozzle if needed.
Fortunately, with the YesWelder MIG gun kit, you don't have to spend a fortune on MIG consumables. With it, you can afford to change contact tips regularly without breaking the bank.
YW-100L Series Lincoln Magnum 100L and Tweco Mini/#1 Replaceable MIG Welding Gun Consumables
However, prevention is more important. You'll want to avoid burnback rather than having to deal with it, spending time and money on frequent replacements. So, we will talk about the causes and solutions further.
What Causes Welding Burnback?
Figuring out what is happening with your contact tip and wire is the first step in eliminating the issue. Next, you will have to understand why burnback occurs.

MIG Contact Tip with Burnback
Photo by @vanthefabricator (TikTok)
The leading causes of burnback in MIG welding are:
-
Incorrect welding parameters (wire feed speed/voltage)
-
Poor wire feed
-
Faulty ground
-
Incorrect wire stickout
-
Damaged, faulty, or incorrectly sized contact tip
-
Incorrect torch distance
-
Poor quality consumables
Let us further explain each cause.
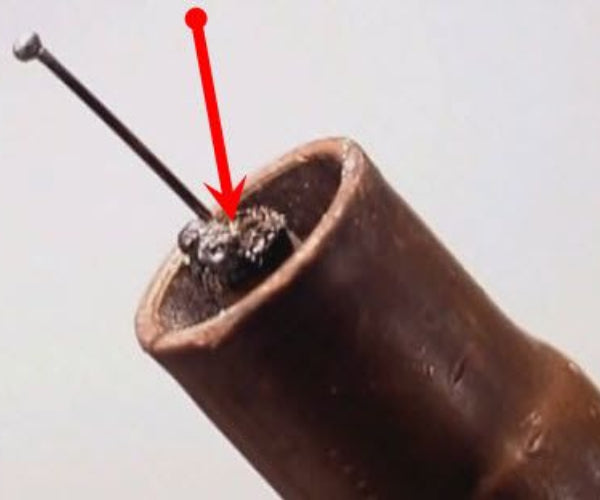
MIG Welding Burnback
Source: https://www.wcwelding.com/mig-welding-tips.html
Incorrect Wire Feed Speed or Voltage
Wire feed speed and voltage are the primary parameters of a MIG welder, and they dictate the heat and the pace of the weld. Getting these parameters right is crucial in producing smooth, deep-penetrating welds. Conversely, using the wrong parameters can cause spatter, lack of penetration, and burnback.
One of the leading causes of welding burnback is low wire feed speed. With low speed, the arc melts the wire faster than it feeds out of the gun. These conditions cause the arc to travel back into the contact tip and fuse the wire with it.

Wire Feed Speed Too Low
Source: https://www.youtube.com/watch?v=Xod-ByrxHg4&t=231s
Poor Wire Feed
Smooth wire feed is crucial in producing uniform, high-quality welds. However, as the wire passes through the feeding mechanism, liner, torch, and contact tip, it can tangle or kink. Long-term poor feeding can damage the wire or the tip, clog it, or create debris.
Among other defects, carved tips, debris, or clogs can cause the wire to burnback and fuse with the tip. Too much tension can peel or damage the wire, also causing it to burn back into the tip.

Adjust the tension properly when MIG welding.
Source: https://www.youtube.com/watch?v=f41Zr_R9oO8&t=337s
Faulty Grounding
In arc welding, an electric arc forms once the circuit between the electrode and grounded metal is closed. Breaking this connection during the welding can cause voltage drops, leading to various issues and inconsistent welding results.
In MIG welding, faulty grounding, a burned ground, or a loose connection can cause voltage drops. The feeding mechanism keeps feeding the wire, but the voltage drop causes the wire to burn back into the contact tip. A faulty earth clamp can affect your safety and welding performance.

Make Sure Grounding Is Proper
Source: https://www.youtube.com/watch?v=sWOiW6NqhT4&t=160s
Incorrect Wire Stickout/Torch Distance
A wire stickout is the wire length between the torch tip and the workpiece. In MIG welding, it is recommended to maintain a stickout of approximately 3/8 to 1/2 inch. The stickout will also dictate how close you hold your torch to the base metal.
Using too long a stickout and holding the torch too far will generate excessive spatter. The wire will spit all over the joint and workpiece, so you want to avoid it. Meanwhile, using a stickout that is too short and holding the torch too close will cause the wire to burn back into the nozzle and contact tip.

Maintain 3/8”–1/2” Stickout when MIG Welding
Damaged or Faulty Contact Tip
As noted, the wire travels a long path from the spool to the MIG gun tip. Each part of the feeding system must be compatible with the wire and the torch you are using.
A damaged or wrong-sized contact tip can cause wire burnback. Trying to force a large wire through a small opening will cause it to clog and fuse with the tip. Damaged, dirty, or clogged contact tips can interfere with feeding and cause wire burnback.

Faulty contact tips may cause feeding issues and burnback.
Source: https://www.youtube.com/watch?v=iWieTM0PKqI&t=160s
Poor Quality Consumables
Cheap, off-brand MIG consumables, such as contact tips, nozzles, and welding wire, can cause feeding issues and burnback. As mentioned, poor feeding leads to inconsistent results and affects the quality of the weld. Cheap fillers can have an inconsistent diameter, damaged coating, and poor feedability, all of which can cause defects or burnback.
Trying to save on consumables can increase the time spent on reworking, cleaning, or replacing them. Therefore, we recommend purchasing consumables from a trusted manufacturer, such as YesWelder.

Choose the Right and High-Quality Consumables
Source: https://www.youtube.com/watch?v=ugeBdO0-iJ4&t=946s
Tips and Solutions on How to Avoid Welding Burnback
Understanding causes was the second step in avoiding MIG burnback, and in the end, we left tips and solutions. Some of the causes are relatively common and simple to fix, but for some, you'll need more effort. So, here are the essential tips and solutions on how to avoid burnback:
-
Adjust the wire feed speed and voltage
-
Check your ground and polarity
-
Check the wire feeder and other feeding components
-
Use the right stickout
-
Provide proper torch distance and keep it consistent across the weld
-
Adjust burnback control
-
Always buy consumables from a trusted supplier
Here are detailed explanations about each.

MIG Welding with the YesWelder DP200
Photo by@ YesWelder (YouTube shorts)
Adjust Wire Feed Speed and Voltage
To prevent burnback, always adjust wire feed speed and voltage according to the metal thickness and wire diameter. Keep in mind that each machine is unique, so always follow the manufacturer's recommendations when dialing in your settings.
If you have issues tuning your welder as a beginner, we recommend getting an MIG machine with smart parameter matching, such as the YesWelder DP200. This feature will automatically adjust wire feed speed and voltage based on metal thickness, wire type, and diameter to give you a head start. However, if you still feel like the wire is burning back, you can always manually increase the wire feed speed to match the voltage.
Check Your Grounding and Polarity
Before welding, check your ground and earth clamp. Overheated copper, damaged wires, or a loose connection cause voltage drops that yield burnback. Therefore, keep your ground connection secure and in good condition to avoid burnback. Whenever possible, ground the piece directly or close to the weld.
Also, pay attention to polarity. MIG welding uses DCEP, or reverse polarity. Your torch should be in the positive terminal, and the earth clamp in the negative terminal of the cycle. For Flux core welding, switch the polarity to DCEN. Using the correct polarity will create the proper metal transfer and eliminate the risk of spatter, erratic arc, and burnback.

MIG Welding Polarity
Source: https://www.kingsofwelding.com/guides/mig-welding-guide/
Ensure Smooth Wire Feed
Check all parts of the wire feeding system to ensure smooth wire feed. Make sure your rollers are the right type and size for the wire. Solid MIG wires work well with grooved rollers, while Flux-cored wires require knurled rollers for smooth feed. The diameter of the rolls and wire should match to avoid slipping or overfilling the rolls.
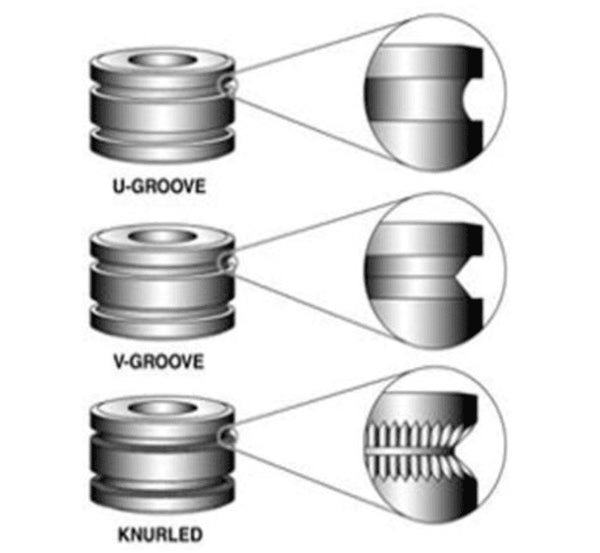
Choose the Right Drive Roller for Each Wire Type
Source: https://bancrofteng.com/how-to-solve-wire-feed-problems-when-welding-aluminum/
Adjust the tension to improve wire feeding and avoid burnback. Too much tension can damage the wire, while too little tension will cause it to slip. Proper tension will, among other things, help eliminate burnback.
Finally, check the liner. It should be free of debris, adequately sized, and well-trimmed. You should replace the kinked, coiled steel liner immediately. Well-maintained and debris-free liners have an average service life of 6-12 months, depending on how often you use your welder.

The liner should be free of debris, adequately sized, and well-trimmed.
Source: https://www.binzel-abicor.com/US/eng/media/ebooks/mig-gun-maintenance-guide/
Use The Right Stickout
MIG welding requires a 3/8-inch to 1/2-inch wire stickout. Typically, 3/8 to 1/2 inch is best for 0.030-0.035” wires you will be using at home. However, industrial-grade, larger wires require a 5/8 to 3/4-inch stickout.
Too long of a stickout lowers the amperage, increases spatter, and raises the risk of porosity. A stickout that is too short increases the heat and causes the wire to burn back into the nozzle and contact tip. Welding too close to the joint also increases the heat exposure and shortens the service life of consumables.

Incorrect Electrode Stick-Out (Too Long or Too Short)
Source: https://www.youtube.com/watch?v=Xod-ByrxHg4&t=231s
Provide a Consistent and Adequate Torch-to-Work Distance
Maintaining consistent electrode extension during welding is critical for producing smooth results. Varying the extension can change the amperage and consistency of the weld and cause burnback.
Although keeping a consistent distance and stickout may sound effortless, it can be very challenging, especially in out-of-position work. Crowding workpieces, uncomfortable positions, clutter, or hard-to-reach places can be a nightmare.
You will have to adjust the gun angle, position, and distance relative to the workpiece. Otherwise, you can expect a lack of penetration, incomplete fusion, tie-in, and burnback.

Keep Consistent and Adequate Torch-to-Work Distance
Source: https://www.youtube.com/watch?v=tpIQkMy3o6I&t=16s
Adjust Burnback Control
Every MIG welder has a built-in burnback, as it would be impossible to weld without it. However, burnback control is a handy feature that many new welding machines, including the YesWelder DP200 Dual Pulse MIG welder, provide. This feature allows you to manually adjust how much wire retracts as you stop the trigger.
The basics of MIG welding require a machine with a built-in burnback. This function keeps the wire electrically live for a few moments after you release the trigger to prevent the wire from sticking to the workpiece. Without it, releasing the trigger would stop the arc and wire feeder momentarily. The wire would stay and fuse with the joint, forcing you to cut it out every time.
That's why all MIG welders have built-in burnback, but only advanced machines allow you to control it. New technology enables welders to fine-tune the amount of burnback. For example, you can reduce the burnback if you feel like you are losing too much wire after each weld. You can also increase the burnback if needed.
However, keep in mind that maxing burnback out increases the risk of wire fusing with a contact tip or nozzle. Contrarily, minimizing it may cause your wire to stick to the joint. Therefore, we recommend starting with the default value and tuning it until you get a sweet spot.

Start with the default burnback value, then fine-tune.
Always Buy Consumables From Trusted Manufacturers and Suppliers
Before buying MIG consumables, make sure they are compatible with your torch, feeding, or wire mounting mechanism. Buying the wrong type, material, or size will cause feeding issues, unpredictable results, and burnback.
When choosing consumables, make sure you buy them from a trusted manufacturers. At YesWelder, all MIG consumables, including nozzles, contact tips, diffusers, and MIG wires, are quality-tested and built according to rigorous standards. MIG wires, such as ER70S-6, follow the AWS standards for reliable composition and quality control, ensuring they have an even diameter and coating across the roll.
ER70S-6/10LB-0.8 .030" 10LB Spool Carbon Steel Solid MIG Welding Wire
Quick Summary of Causes and Solutions for Welding Burnback
Instead of a typical conclusion, we will finish the article with a quick overview of causes and solutions. Here is a helpful table on what causes welding burnback and how to deal with it.
Cause |
Solution |
Wrong Parameters |
Increase wire feed speed. Adjust WFS and voltage according to the metal thickness. Use smart MIG settings. |
Erratic Wire Feeding |
Check drive rolls and the wire feeder. Adjust tension. Check and replace worn, kinked, or damaged liners with debris. |
Poor Grounding |
Check the earth clamp for damage or overheating. Provide a reliable earth connection. Check polarity. |
Short stickout |
Use 3/8 to 1/2 inch wire stickout. Keep the distance consistent through the weld. |
Foul contact tip |
Replace damaged or clogged contact tips, Use the right size and type for your torch and wire diameter. |
Adjust burnback control |
Check and reduce burnback control if your welder allows it. |
Poor quality consumables |
Choose consumables compatible with your torch and welder. Always buy consumables from a trusted manufacturer and supplier. |
🧐How to Avoid Welding Burnback: Causes and Solutions FAQ
Leave a comment